case studies
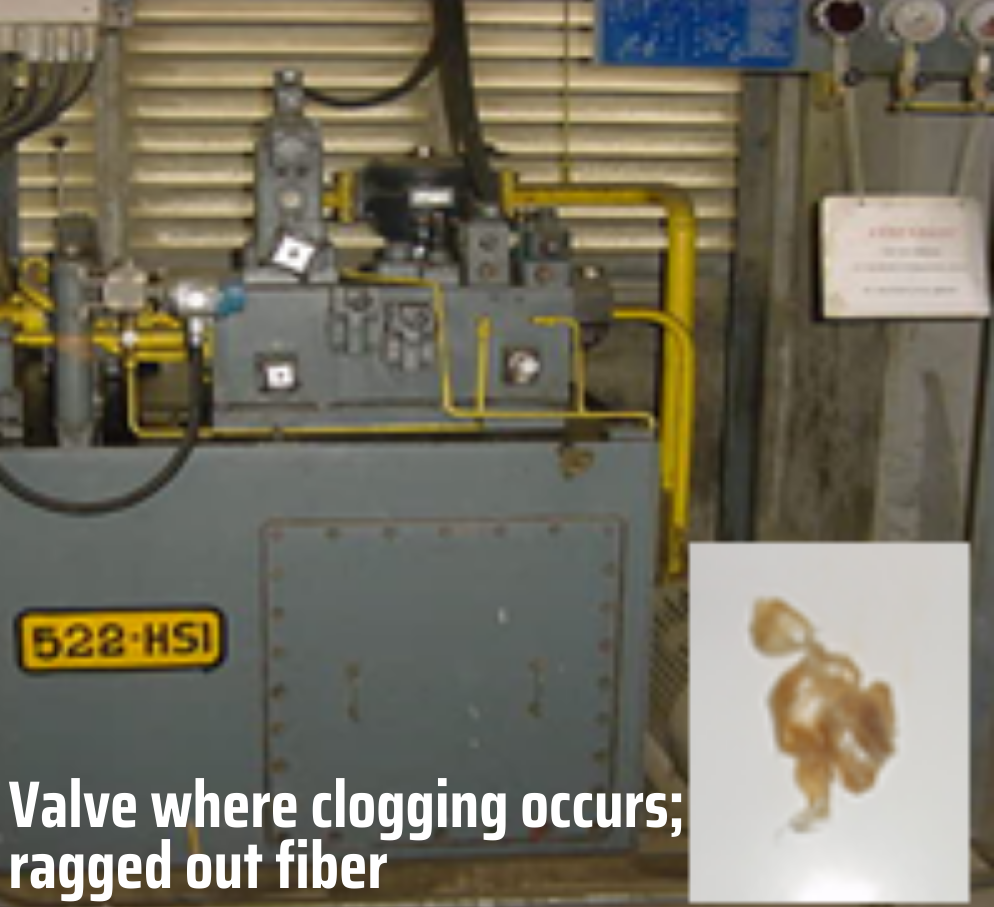
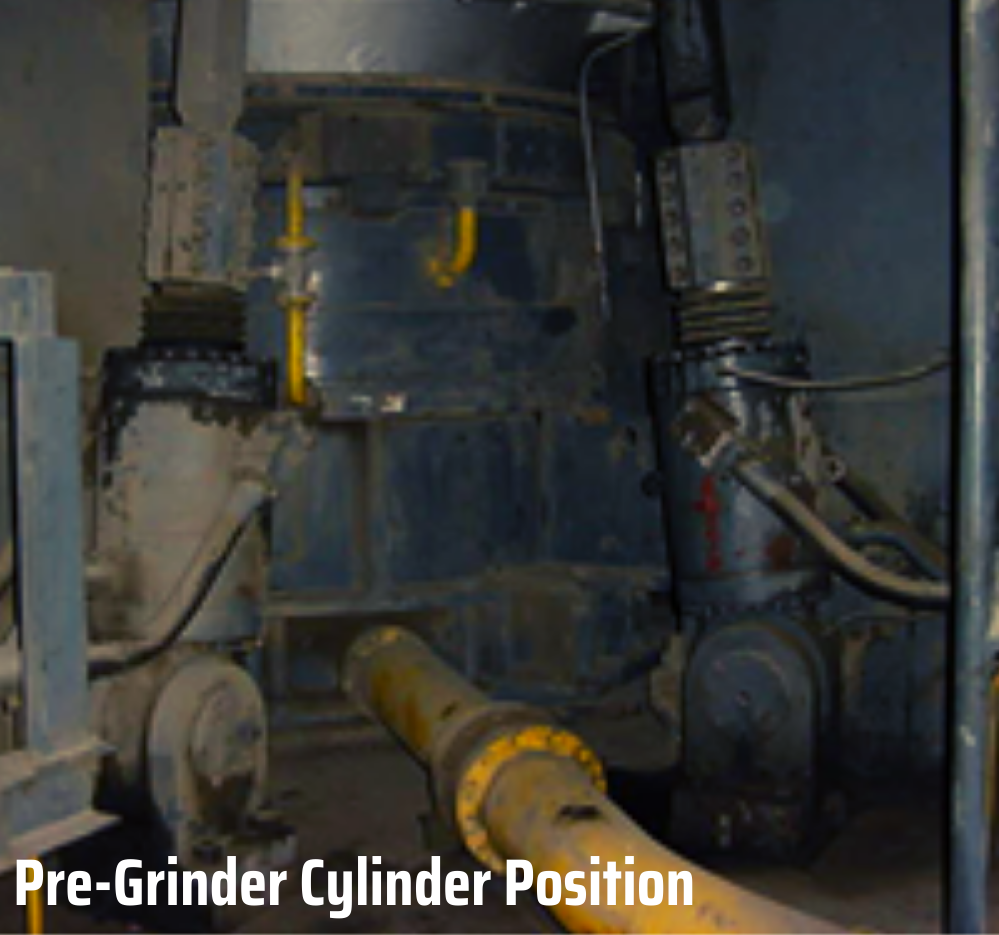
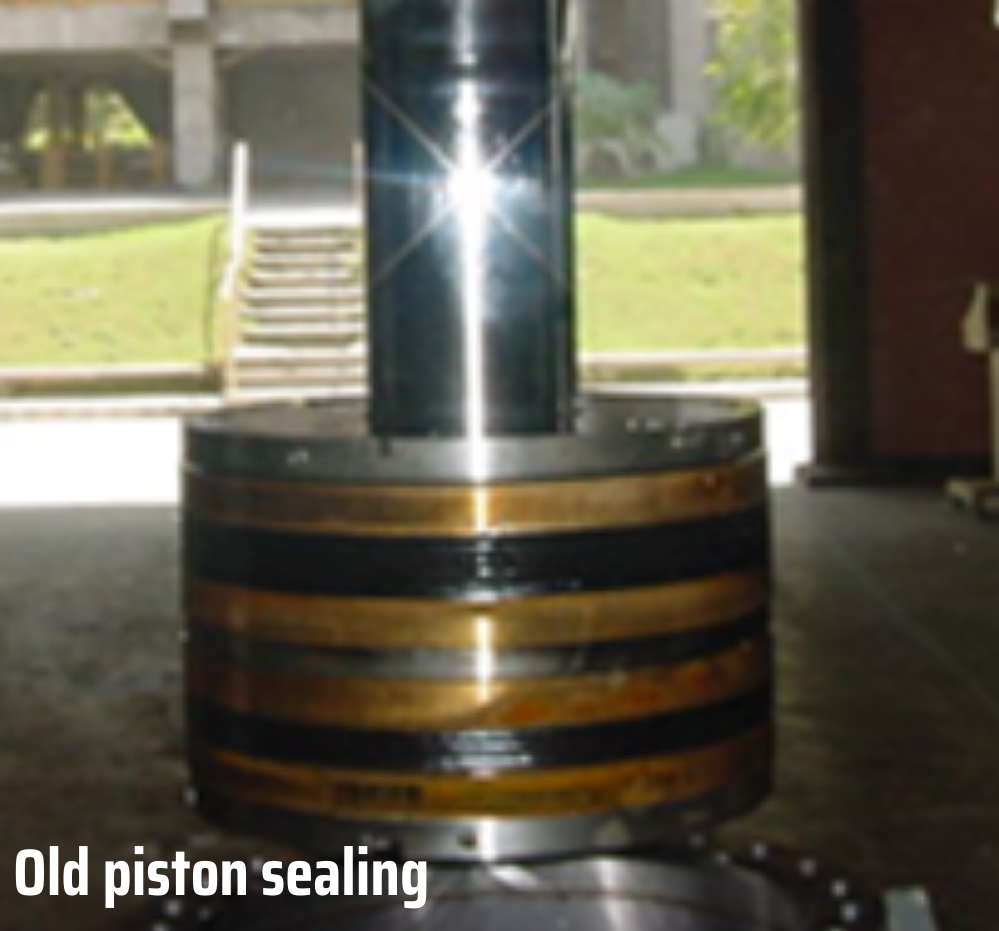
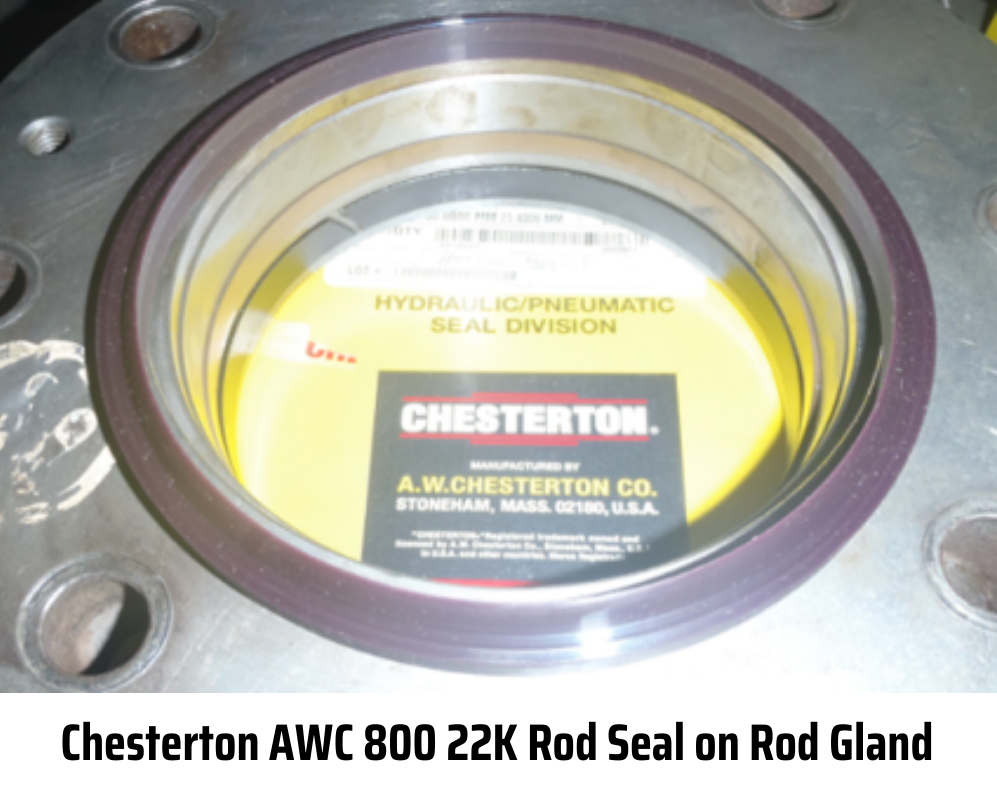
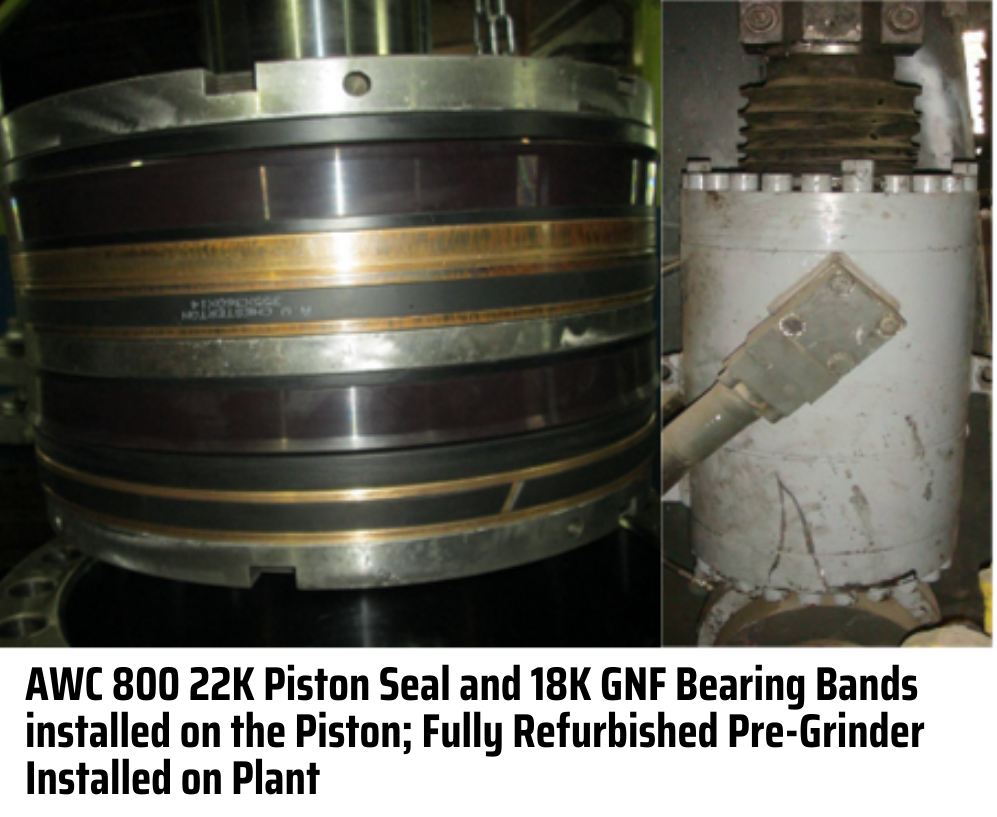
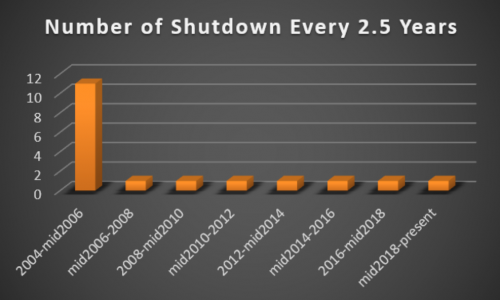

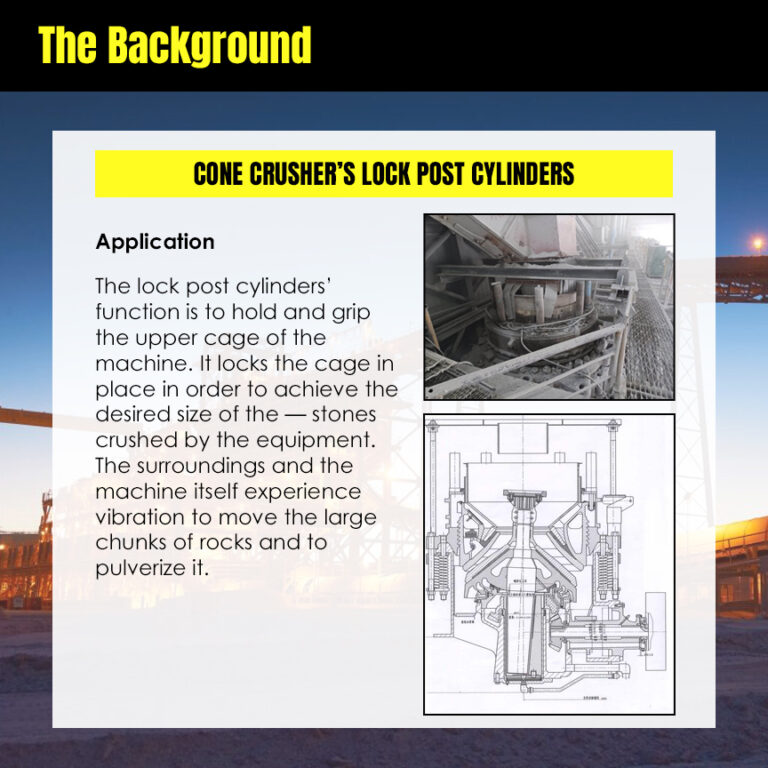
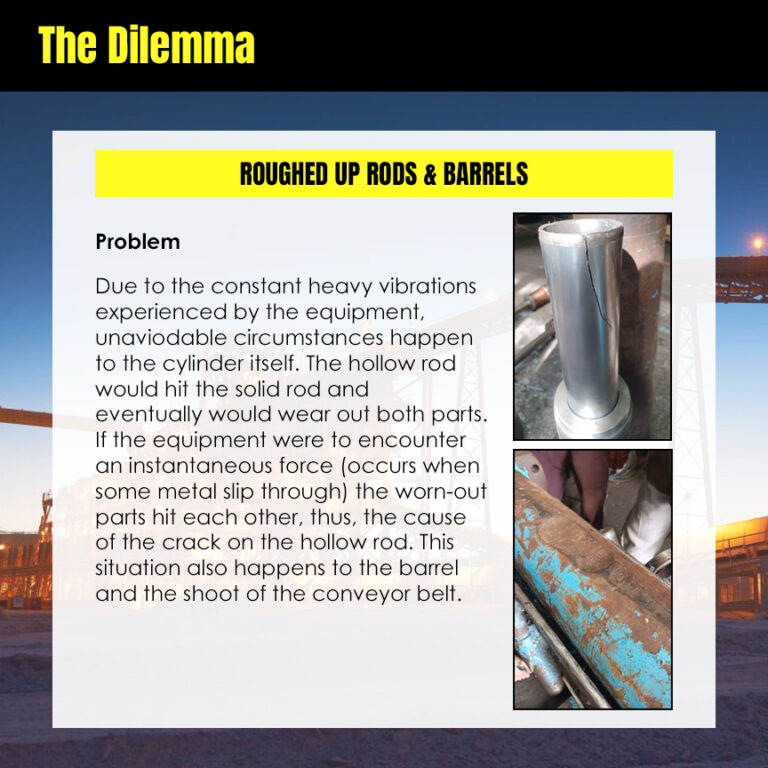
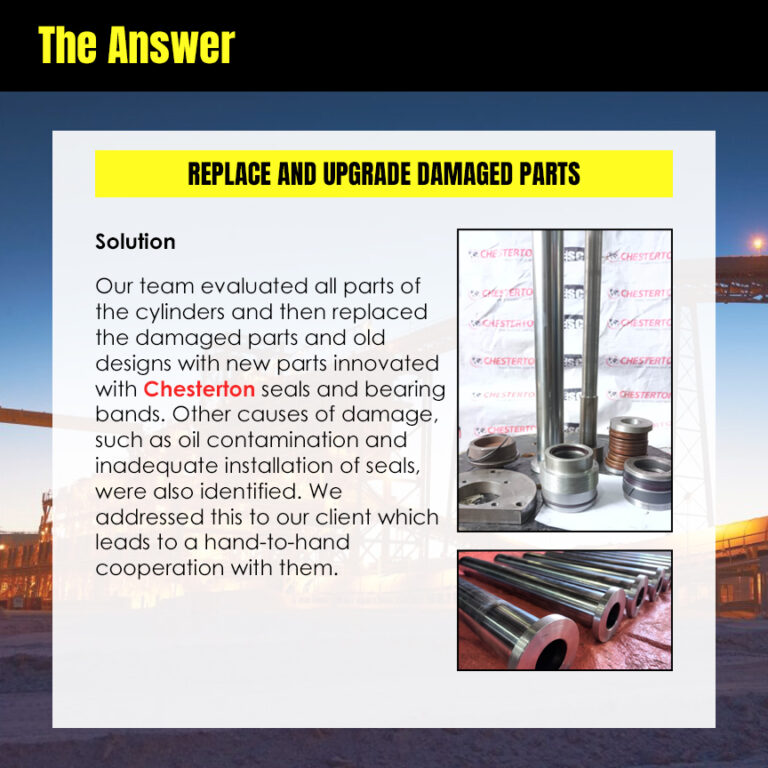
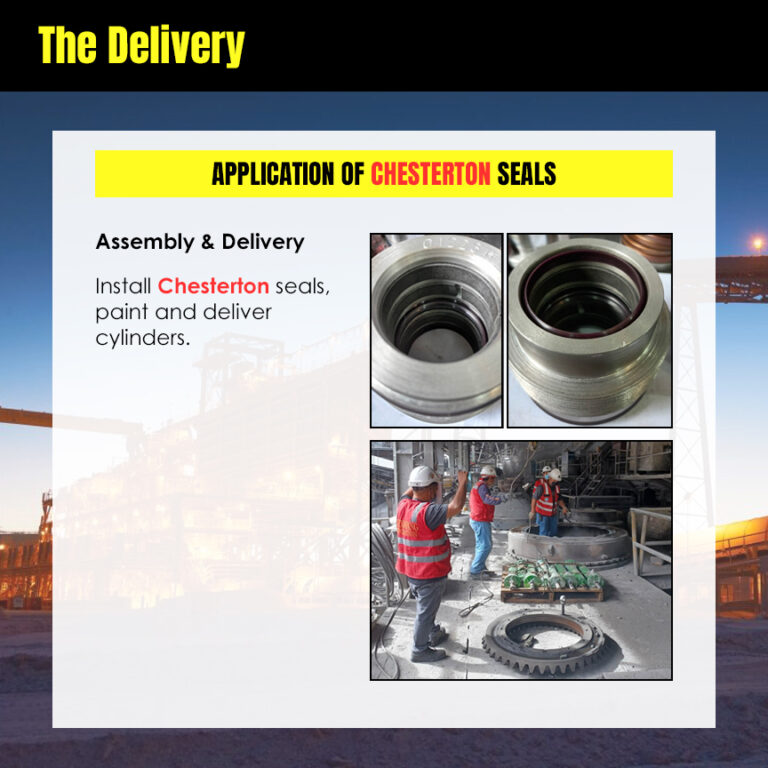
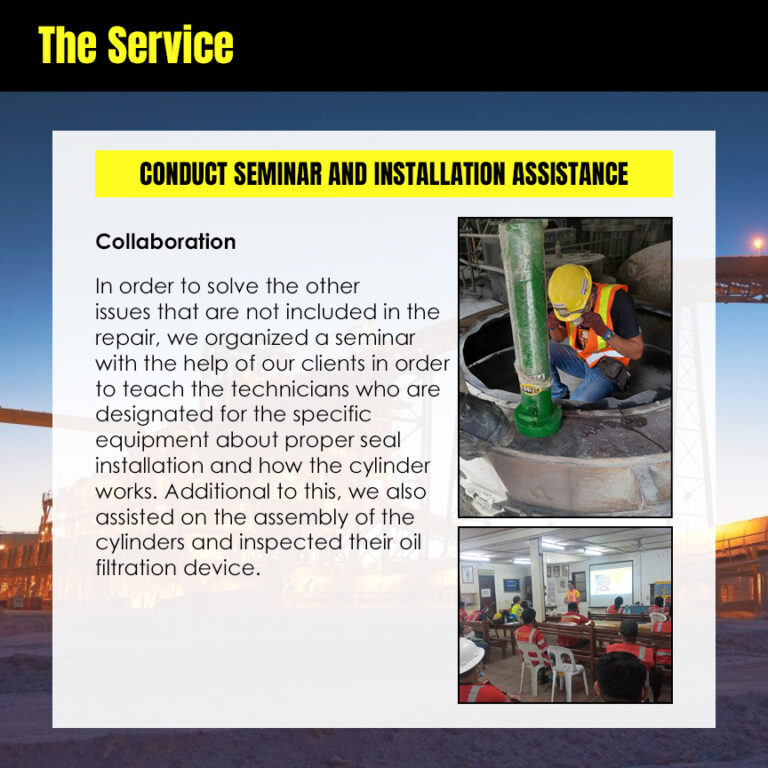
Previous
Next

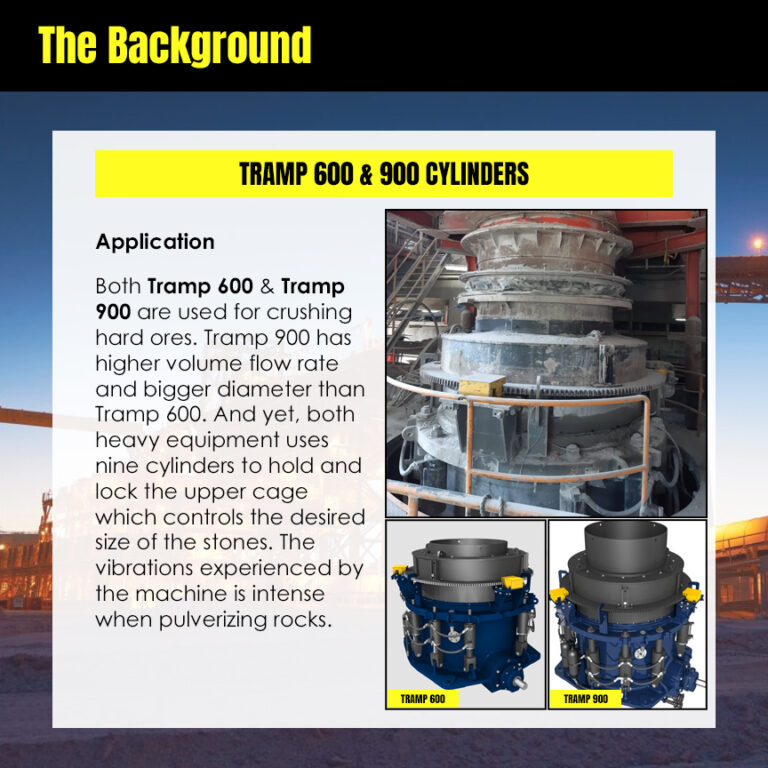
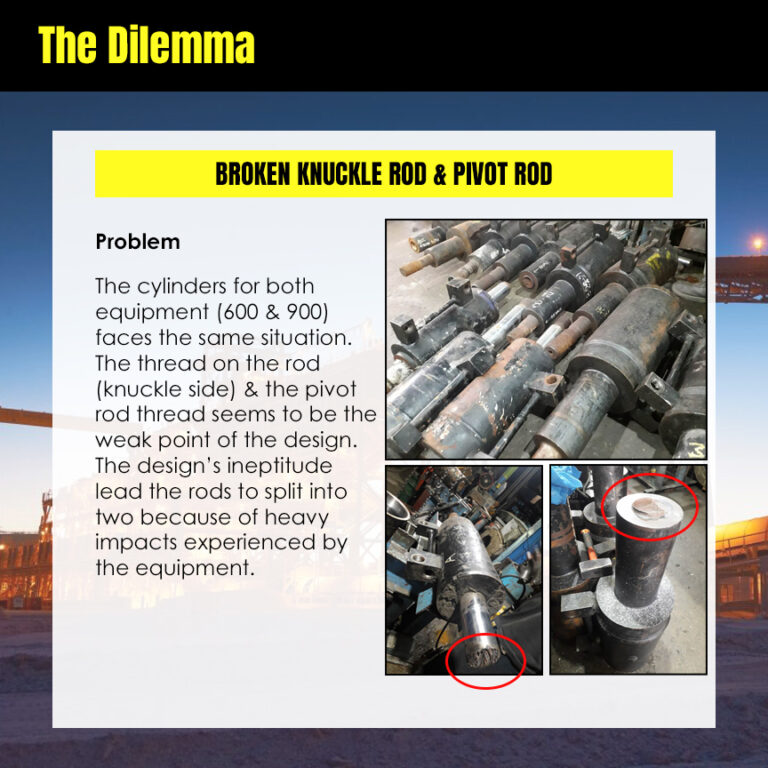
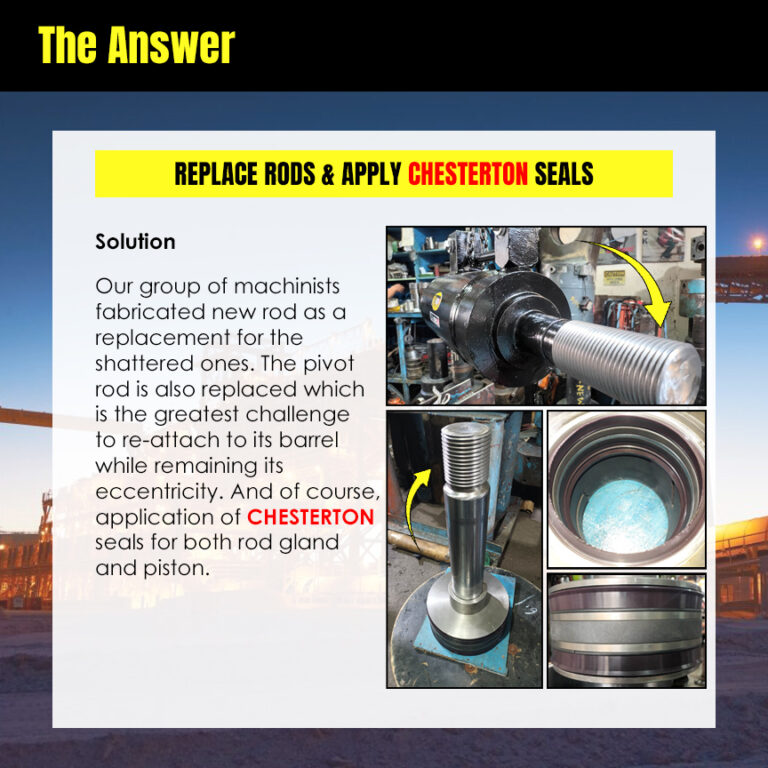
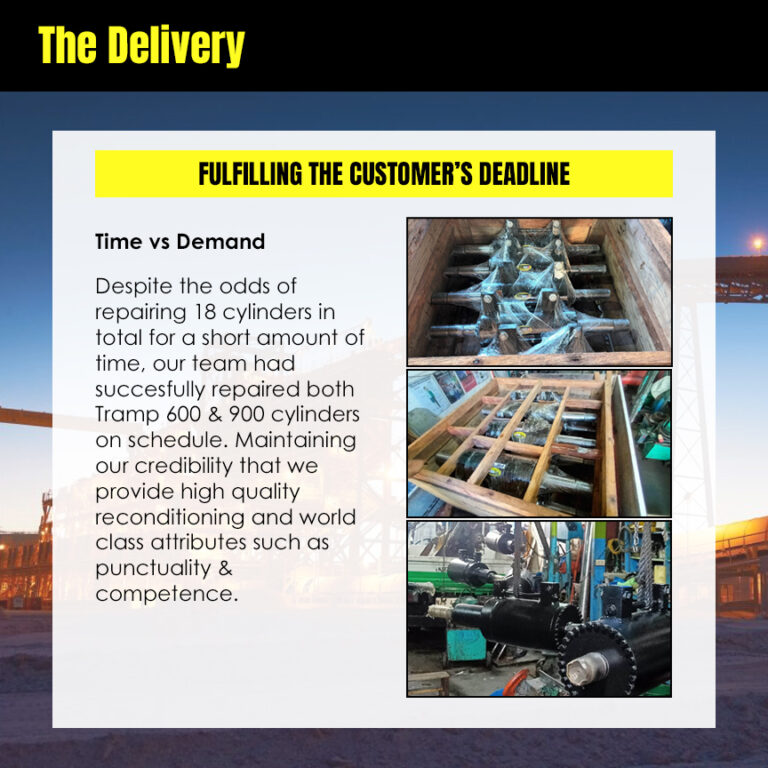
Previous
Next

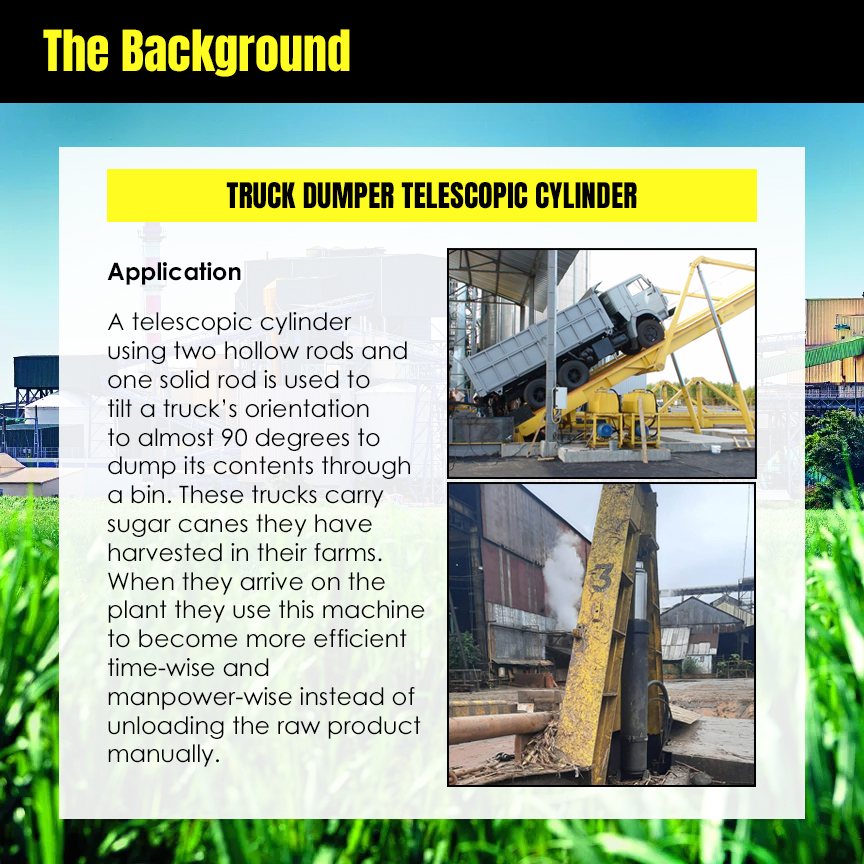
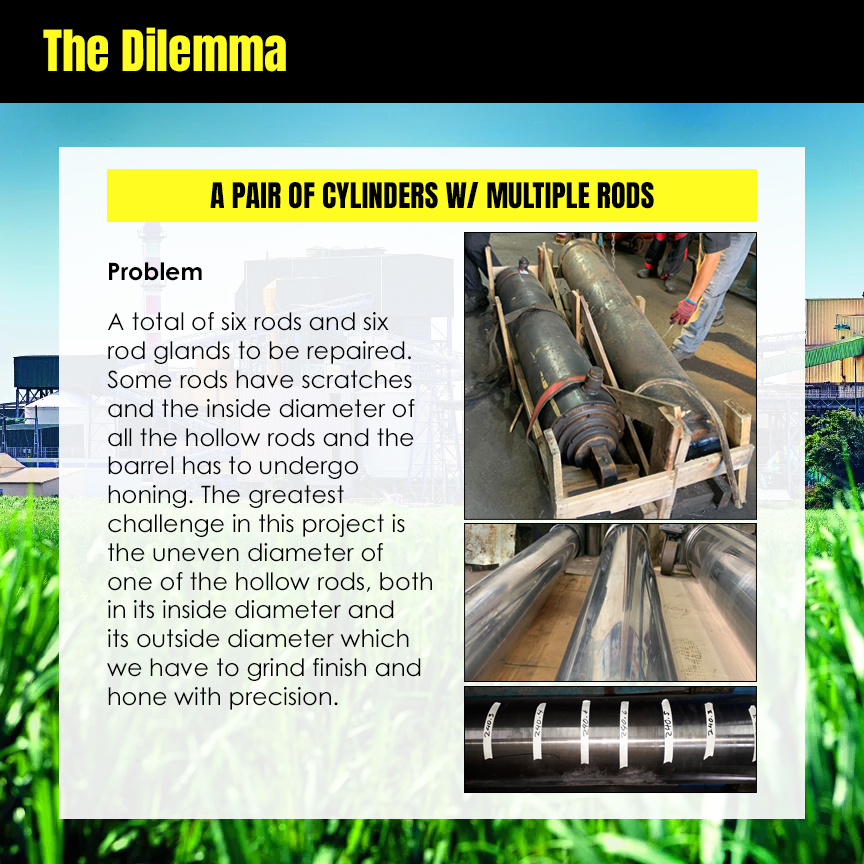
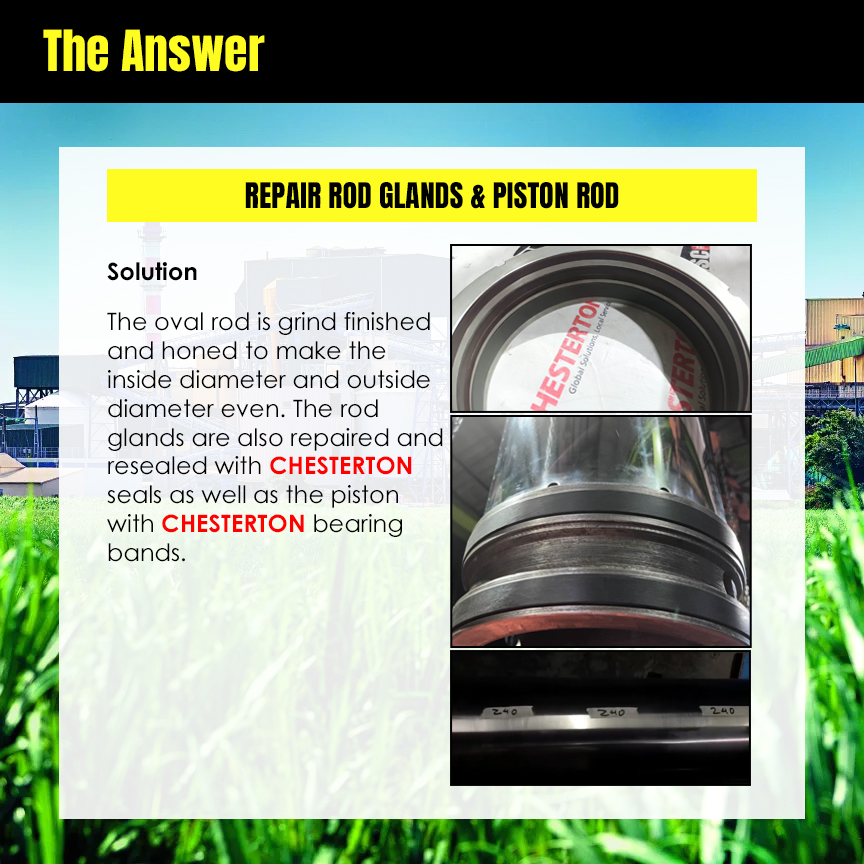
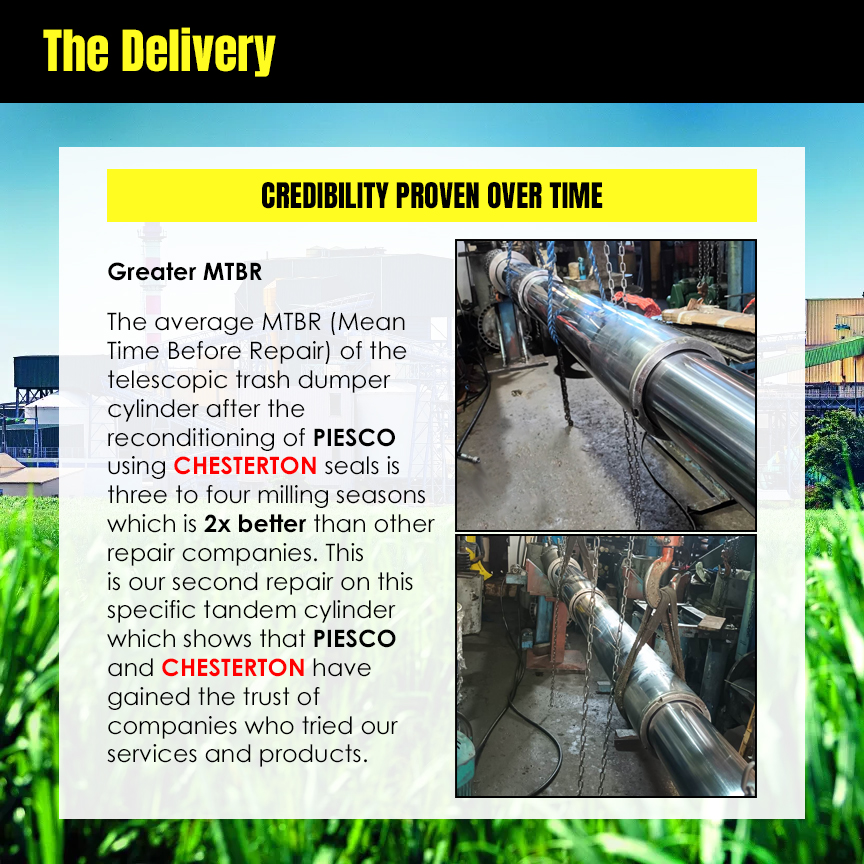
Previous
Next

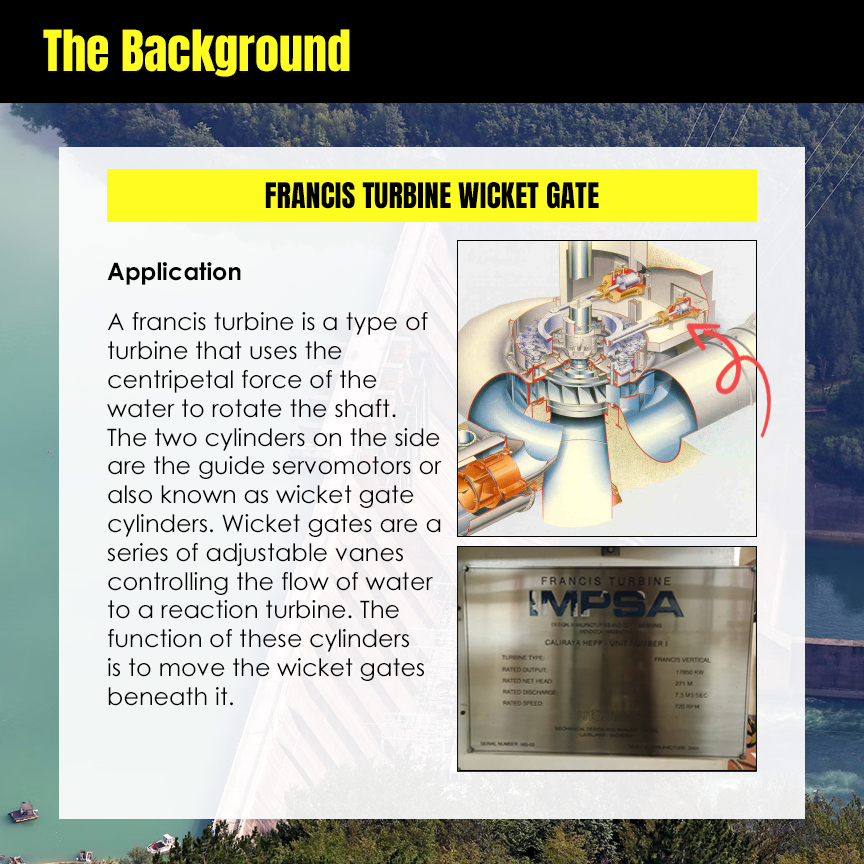
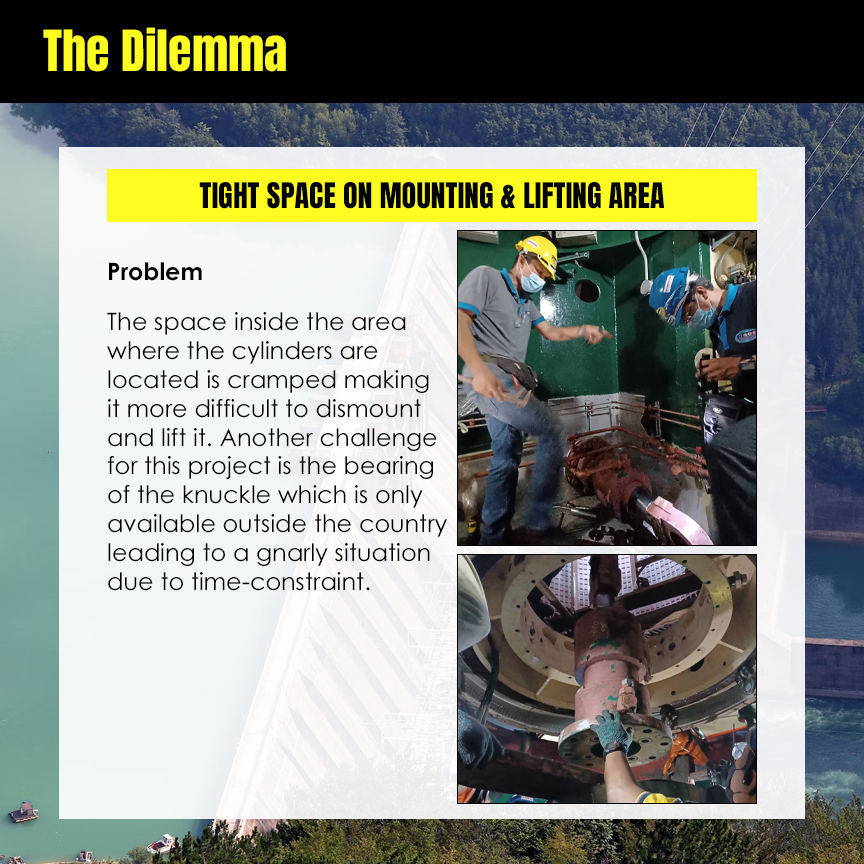
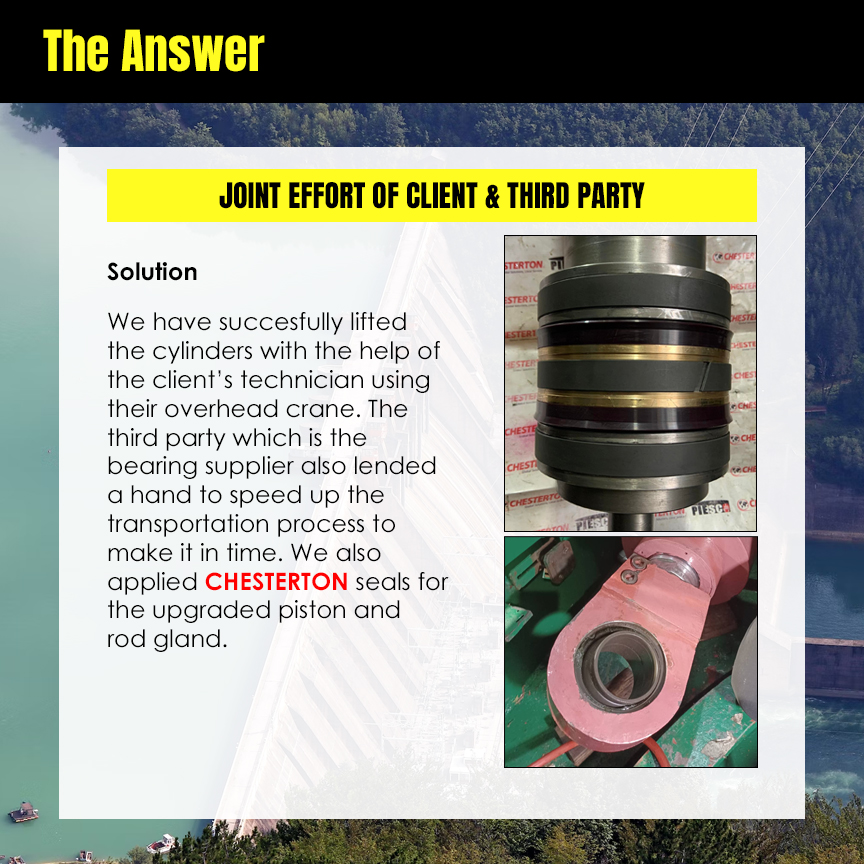
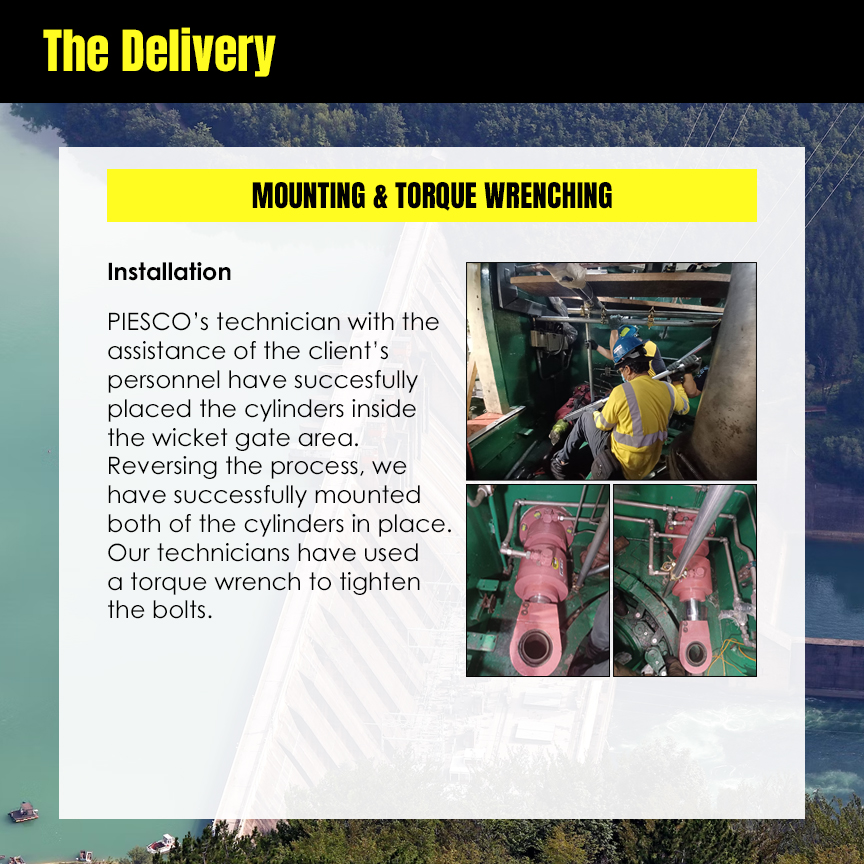
Previous
Next